最近の動向

1 顧客ニーズの変化
近年熱間鍛造も精密化が進み、高速成形可能なスクリュープレスの特質から、温間域での鍛造にも用途が拡大し、よってプレスに対する高精度化の要求も高まって来ている。最近指摘されている要望は下記が上げられる。
(1) 加圧エネルギーのより均一化
スクリュープレスでは加圧時にフライホイールエネルギーがすべて消費され、フライホイールの回転数制御によって加圧力の大小を調整する。(ハンマーの落下速度の調節で加圧力を制御するのと同じと考えて差し支えない)従来の摩擦駆動方式(フリクションスクリュープレス) では、フライホイールの回転をエンコーダーで検知して回転エネルギーを制御する方式が採用されてから加圧力の繰り返し精度は格段に向上した。しかしながら摩擦クラッチ部の熱変動で、クラッチオンの際の起動特性が変化してしまい(起動カーブの角度が変化する)クラッチオフのタイミングがずれ、若干のエネルギー変動が起きてしまう事が指摘されていた。たとえば完全自動運転時、定常運転中はほとんどエネルギー変動はないが、チョコ停の停止の間にクラッチ板( フリクションホイール) が冷却されてしまい、再起動直後のエネルギーが変動してしまう様な事が起こる。
(2) クラッチライニングの長寿命化
摩擦部が線接触であるため、ライニング材には柔軟性・耐熱性が要求され、一般に天然皮革(牛・水牛等)が使用されているが、保革処理をしすぎると寿命は保てるがパワーが出ず、保革処理をしないと起動性は良く加圧のバラツキが少ないものの寿命が短くなる。連続運転では機械はなるだけ停止させたくないので、この問題解決は大きな要望事項である。メンテナンスコストは低減が強く要求されている。
(3) 最適な稼働率
このプレスはフライホイールエネルギーを成形時にすべて使用するのでパワフルであるが、反面大きな機械で小物を加工する場合、フライホイールの回転を落としてエネルギーダウンさせないと過負荷となってしまうので稼働率が下がってしまう欠点も持ち合わせている。
(4) これらの要求のほとんどを解決したものが、サーボモータ駆動スクリュープレスである。
このプレスはフライホイールエネルギーを成形時にすべて使用するのでパワフルであるが、反面大きな機械で小物を加工する場合、フライホイールの回転を落としてエネルギーダウンさせないと過負荷となってしまうので稼働率が下がってしまう欠点も持ち合わせている。
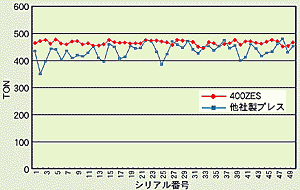
(a)
基本的にサーボモータでフライホイールの回転数を直接制御するので、毎回加圧直前のフライホイール回転数とエネルギーにばらつきは発生しない。自動運転中の加圧力のばらつきについて、従来のフリクションスクリュープレス(他社製)とサーボ駆動機との加圧力のばらつきの比較を図で示す。
備考: サーボ駆動機の場合、ラム速度を計測すると鍛造前の速度はほとんど均一です。添付した加圧力のグラフでのサーボ機の荷重ばらつきは、素材のボリュームや素材加熱温度、潤滑条件などのばらつきをも含んだ形で出てくるので、グラフでの荷重ばらつきはプレスのエネルギーばらつきでは無いという見解が出来ます。
(b)
摩擦駆動では無いので当該消耗部品が無い。(汎用サーボモータを使用する機種においてはモータをフライホイールに連結するベルトの消耗はあるが、寿命は数年あり規格品が安価に購入可能である)
(c)
小さな加圧力セットの場合、スライドは高速でアプローチした後減速し弱打するプログラムが自動的に実施されるので、大きなプレスで小さな素材を鍛造しても一行程の時間が長くなる事が無い。なお上昇時の加速・減速・上限での停止も最速で、なんら調整の必要も無く運転される。
2 新規開発されたスクリュープレスと、装置・工法
以下に記載するサーボモータ直動システムの導入により、従来の摩擦クラッチ駆動形式はその歴史的使命を終了した。高速化などの目的の為に、4ディスク型超高速フリクションスクリュープレスやダブルスクリュー形式などの開発がなされたが、これらも基本的にサーボ駆動形式に取って変わられつつある。従って本節では摩擦クラッチ式開発機の記載はせず後編の機種説明での記載にとどめることとする。
(1) サーボモータ駆動スクリュープレス

世界に先駆けて、鍛造用スクリュープレスを汎用サーボモータ駆動方式として開発した。サーボプレスは一般にモータをクランク軸に直結し、スライドの位置・速度・トルクを刻々制御する方式の機械であるが、弊社の開発機はフライホイールの回転エネルギー制御をサーボ駆動化したもので、フライホイールエネルギーは従来のフリクションスクリュープレスの様に加工時すべて消費され、場合によっては30kW のサーボモータで公称能力3000kNを出すこともできる(軸直結型であれば30kWでせいぜい700~800kN どまり)。加圧は従来のフリクション駆動型と同じ瞬間的な衝撃加圧となり、時間・加圧トルク・加圧速度の時間に応じた制御はできない。つまりフライホイールエネルギーのすべてを消費して加圧する従来の形態に変わりが無く、パワフルな鍛造加工ができる。スライドが下降して鍛造する一般機とともに、上昇して鍛造するアプセット加工スクリュープレスにもサーボ駆動が導入されているが、以下解説する総てのスクリュープレス機がサーボ駆動化されている。特長としては次項があげられる。

300 VES
400 ZES
省メンテナンス
摩擦駆動でなくクラッチに相当する部品が無い。通常の運転ではブレーキは作動せず、モータ自体がスライドを停止させる。メカニカルブレーキは停電時などの非常用であり、従ってブレーキライニングは摩耗が無く永久使用である。摩擦駆動機の摩擦ディスク・シャフト軸は存在せず摩耗する部品が無い。構成部品が極端に少なく、従って総合的に保守が著しく低減される。
省エネルギー
モータは常時回転せず、稼動時のみ回転する。(フリクション式では常時モータは回転する)一行程終了時、スライド上昇から停止に至る部分の停止動作はモータ自体が行い、この際回生電力を発電し電気を工場内に押し戻す(その電力分、工場内で消費する電力が減る)。またフリクション式と比べ、モータは常に回転しないので、総合的省エネ効果は従来のフリクション駆動機と比較すると30~50%の消費電力が削減される。
スライドが減速
スライドが減速でき、対象ワークサイズが広範囲摩擦駆動機ではスライド加速後減速動作は出来ないが、サーボ駆動は直動であるのでこれが可能で、大きなプレスで小さなワークを鍛造しても1ストロークの加工時間がほとんど変わらず、プレスの大が小を兼ねる事が出来るという画期的な効果が出た。加圧エネルギー設定により、スライドは下降を始めた後加速し、その後減速してから設定されたエネルギーで素材を加圧する。すべて自動で行なわれる。加圧直前のフライホイールエネルギーは極めて均一であるので精度良く鍛造できる。
運転の応答性が良い
直動であるのでクラッチの応答時間に要する時間ロスが無く、運転応答性が良い。インチングではなくジョグ(緩速)運転モードとなり、金型のセットが極めてやりやすい。
静加圧を持続的
静加圧を持続的にかける事が出来、スライドの位置と速度制御が可能な機種もある。
(2) たてアプセットスクリュープレス(サーボ駆動)

写真1 逐次鍛造品
従前から「ビンセント型スクリュープレス」と呼ばれていた機械を、内容がわかりやすい様に名称を改めた。スライドをネジ機構により引き上げてから加圧する特異な構造を持ったスクリュープレスで、長い材料の頭部だけの鍛造(アプセッティング)に大きなメリットがある機種である。昔から太物・長尺ボルトの頭の部分の熱間鍛造(六角あるいはキャップスクリュー)に好んで使われてきたが、操作に極端な熟練を要していた物をサーボ駆動化して近代プレスとした。(サーボ機の前に、電子・空圧制御方式のフリクション駆動型を開発し好評を得ていたが、サーボの開発完了により、生産機のほとんどがサーボ化した) アプセット工法は、軸端を鍛造で膨らませて成形する塑性加工である。基本的にはかなり長い材料が投入される事と、座屈させない工法をとる事の2点に留意すれば良い。軸付歯車、ボルト、リアアクスルシャフト、エンジンバルブ、2輪ハーフクランクなど多くの製品が鍛造されている。長軸物の塑性加工は座屈に配慮しなければならず、一般に3~5工程の逐次鍛造加工がされている。(写真1)

写真2
サーボ駆動たてアプセット
スクリュープレス
写真3
3次行程逐次鍛造用上シフト装置
スクリュープレスの最近の動向 アプセット加工には従来、機械プレスであるヘッダーや横型アプセットマシンが用いられ、工程ごとに必要な金型、トランスファー装置、型締め装置が必要であるため、高価な鍛造加工として位置づけられていた。弊社で開発した装置は、従来、ビンセント型フリクションプレスと総称され、太物熱間ボルトや犬くぎの鍛造に重宝に使用されていたもので、これをサーボモータ駆動化し、より精密な鍛造加工を可能とした。(写真2) 成形エネルギーが大きいので、3000kNのプレスで2インチの六角ボルトの頭部を成形する事ができる。
●プレスのスライドは下から上に向かって動いて鍛造する。カウンターブローに類似している。一般にストローク長さが大きく設計でき、ストローク長さは600~800mmであり、長い材料が投入できる。なお、下型スライド装置を装着すれば床に穴を掘った深さ分の材料長さが選定できる。
●材料のトランスファーが必要ない。材料を入れると、1打目、2打目、3打目ごとに自動的に上型が移動して鍛造する。それぞれの加圧エネルギーは別々に任意に設定でき、鍛造を繰り返す。材料を下型に入れ、スタートボタンを押せば最終工程の鍛造まで自動的に加工される。勿論材料挿入装置と取り出し装置の取り付けで全自動化できる。(写真3)
およそ考えられる熟練工の複雑な運転操作をモード化し再現可能とした。たとえばスライド上昇途中の中間停止・再発進・加圧・スライドの戻りとノックアウト・スライドを少し上げての材料の投入などである。スライドストロークのすべての位置で信号発信の接点を取ることができる。
●金型費が安い。下型は1つですみ、上型は2~4型程度であるので必要な金型数が少ない。プレスに機構的下死点(当該機では上昇して加圧するので加圧端と呼んでいる)が無いので上下金型の総合厚みは基本的に任意に設定でき、型の修正彫り下げはそれぞれ任意の値であっても何ら支障無い。
●段取り時間が短い。加圧端がなく、全金型の組合わせ厚みの考慮がまったく必要ない。メカニカルプレスのような下死点調整の必要がない。工程ごとの加圧エネルギー調整をするだけである。うまくすると最初の一本から良品を出す事も不可能ではない。
●割り型でないので、製品に縦筋が付かない。
●直動式で摩擦クラッチがない。ブレーキは非常用のいわばパーキングブレーキで、ライニングは半永久的であり、交換に関わるメンテナンスが必要ない。一行程終了時の停止はモータ自体で行い、この際発電される回生電力により3~5割省エネになる。摩擦クラッチ式では不可能な行程途中のスライドの減速が可能で、一行程の所要時間は加圧力の大小にかかわらず殆ど最速一定である。また、直動であるので加圧力のばらつきはない。
●メカニカル横型アプセットマシンと比較しておよそ半額以下と推定する初期価格と、金型費削減、メンテナンスコスト削減により、割安なアプセット鍛造が可能となった。この形式が設計構造上アプセット鍛造に有利な事は、ストロークが長くできること、材料の金型からの突き出し量を簡単に微調整できること(ピンの入れ替えの必要が無い)、ノックアウトは叩き出しで、油圧などの他の駆動源が必要無いこと、ノックアウトバーやピンが簡単に取り出せる事などであり、他のいかなるプレス機械・一般のスクリュープレスとも非常に特異な構造を持っている。今後も応用用途の拡大が期待される。なお、上型移動装置のひとつにトリミング機構を入れた装置は特許申請中である。
(3) 中空鍛造用スクリュープレス
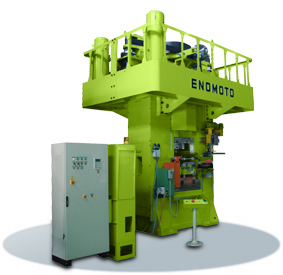
材料の歩留まり向上と、後加工の省略・短縮、鋳造からの移行を目的として開発された、複合装置を組み込んだスクリュープレスである。
スライドが下降し、上型と下型が密着して材料を挟み込んだ後に、材料側面に穴を成形するピン(1~4本程度)が水平方向から飛び込む方式をとる特殊装置(中空装置あるいはサブプレスと呼ぶ)をベッド上に組み込んである。中空装置は取り外し自在で、外せば普通のスクリュープレスとして使用できる。
一般に黄銅(真鍮)や銅、アルミ熱間鍛造で使用される。中空装置はボルスター部のクッションと、クッションの上下運動を水平運動に置き換えるメカニカルカム機構、内蔵されたノックアウト装置から構成される。上型部のみに中空部を作る場合は上型部分にもクッション装置を組み込む事が出きる。メカニカルカム機構のため、金型の上下運動と水平方向の押込みピンの運動が完全に同期するので水平ピンの折損を防止する事ができる。またスクリュープレスの構造上、クッションのストロークエンドまで圧縮するので水平ピンの押込み深さのばらつきが無い。メカニカルプレスでは機構的下死点があるが為、フレームの伸びに起因するスライド下限におけるダイハイト寸法の変動で押込み深さが変わってしまう。材料に変形を与えるエネルギー量が大きいので、フライホイールエネルギーを大きく設定してあるが、基本的構造は一般のスクリュープレスと変わりが無い。

中空鍛造装置
サーボ駆動スクリュープレスにオートハンド・アンローダーを付け、加熱炉とセットとした全自動装置もある。
(4) 両軸端同時加工用スクリュープレス

両軸端アプセット装置
軸の両端を同時にアプセット加工する装置を組み込んだスクリュープレス。基本的に前項の中空鍛造装置の2方向だけの物で、押込みエネルギーが大きいので剛性を高めている。一般に両軸を膨らませる加工の場合、まず片側の軸のアプセット加工をし、次に割型を用いて反対側の軸を鍛造するという手間のかかる加工をしなければならず、もちろん自動化も不可能である。この装置を使用すれば一回の鍛造で両軸がアプセットでき、大きなメリットがある。
(5) 自動割型装置付きスクリュープレス

自動割型装置
左右に開く割型を、自動的に閉じたり開いたりして上下から加圧ピンを押込んで加工する閉塞装置を組み込んだスクリュープレス。加圧時の型締め機構により型の開きを防止する。材料を潰しこみながら型を閉塞する装置は特許申請中である。
(6) 薄板熱間鍛造とマグネシウム

マグネシウム鍛造品
最近板金プレス加工の分野で、薄板を加熱し板の要所要所の厚みを自在に変更させる試みがされているが、一般の機械プレスでは下死点があり、フレームの伸びにより薄い材料を加圧する事には無理がある。油圧プレスではかなり大きな能力のプレスでないと成形しきれないし、加圧する時間が長くなり、材料の温度低下や型寿命が短くなる欠点がある。一方、下死点の無いスクリュープレスではこの様な作業はコイニングの延長線上としてとらえる事ができ、フレームの伸びを考慮する必要の無い事からも最も適切なプレスとして考える事ができる。写真はマグネシウムの薄板を熱間で押しつぶし、後方押出とボス出しを実施したもので、これもスクリュープレスの特質を上手く使用したものである。
(7) マグネシウム素材開発
廃マグネシウムチップを押し固めた後、加熱押出をして棒材やパイプが製作できるが、押し固める前に、素材の結晶粒微細化を図るために、俗称「餅搗き」工程をスクリュープレスで実施して好結果が得られた。平パンチで下型内のマネシウムチップを高速衝撃加圧で押し固めた後、先の細いパンチが入れ替わり、高速で押し固められたマグネシウムチップに押込む。さらに平パンチで押し固める。この繰り返しを何回か実施した後、下型を反転させ、再度同数回押込みと平押し工程を実施する。これにより結晶粒が微細化され、押出した棒材が高強度となった。ラム速度の速いスクリュープレスの特質が効果をもたらしている。(本件は、平成15年度大学発事業創出実用化研究開発事業として採用され、東京大学他数企業と共同実験した)
(8) 半密閉温間鍛造

(株)クリアテック製の金型で製造された温間鍛造品
スクリュープレスは鍛造成形スピードが500~1000mm/secときわめて速く、金型と材料の接触時間が短い事から金型の寿命を長期間維持できる。さらに最も重要な事は、高速成形により発生する加工変形熱と、最初の素材温度が相乗し双方の熱により材料温度が低下する前に狭い金型コーナー部への材料の張り出しをし、全体の成形圧力が下がり、金型の圧力負担を低減させる事が可能となる。半密閉温間鍛造システムとして、この分野で実力のあるクリアテック社製金型とスクリュープレスとのハードソフト両面の提供を実施している。
(9) トリミング装置


トリミング装置
たてアプセットスクリュープレスは、上シフト装置を付けて上型が最高で3個入れ替わることができるが、その内の1個にトリミング装置を組み込んだ。一打目(および二打目)にて鍛造を行い、最後に入れ替わった上型で横バリをトリミングした。スライド速度と停止位置が極めて微細に調整できるので、サーボ駆動方式機にて採用した。